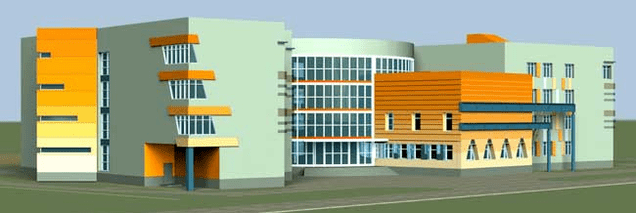
Ahorro de energía en la empresa: las direcciones principales:
- Ahorro de energía eléctrica
- Reducción de pérdidas de calor y vapor.
- Reducción de pérdidas en líneas de vapor
Ahorro de energía en la empresa: métodos de ahorro de energía
- Selección de la categoría de precio óptima y revisión de los términos contractuales de suministro de energía.
- Optimización de motores eléctricos
- Instalación de VFD
- Optimización de sistemas de aire comprimido
Elegir la categoría de precio óptima para la fuente de alimentación
En total, hay 6 categorías de precios de suministro de energía, según las cuales las empresas pueden comprar electricidad a proveedores garantizados.
Todas las pequeñas empresas con una capacidad instalada de menos de 670 kW, en el momento de celebrar un contrato para un suministro de energía automático, entran en la primera categoría de precios.
Todas las empresas con una capacidad instalada de más de 670 kW entran automáticamente en la tercera categoría de precios.
Las categorías de precios primera y tercera no siempre son las categorías de suministro de energía más óptimas y más baratas.
En algunos casos, cambiar a una categoría de precios diferente puede reducir el costo de la electricidad entre un 5% y un 30%.
El tema de las categorías de precios es bastante extenso, en nuestra revisión sobre categorías de precios, contamos en detalle cómo calcular y elegir correctamente la categoría de precios de la fuente de alimentación.
Además de las categorías de precios, también recomendamos observar de cerca otros aspectos del contrato de suministro de energía:
- Nivel de voltaje,
- energía,
- tarifa de transmisión de electricidad.
En nuestra revisión, puede obtener información sobre estos y otros métodos para reducir los costos de energía.
Ahorro de energía en la empresa: motores eléctricos
Es necesario tener en cuenta todos los equipos donde se utilizan motores eléctricos:
- zapatillas,
- compresores,
- aficionados,
- Herramientas de máquina,
- líneas de producción.
Plan de control de motores eléctricos
El plan de control de motores debe convertirse en una parte integral del programa de conservación de energía de la planta.
Dicho plan ayudará a implementar un sistema de ahorro de energía a largo plazo para todos los motores eléctricos de la empresa.
El plan de control de motores asegurará que no ocurran fallas y mal funcionamiento, y si ocurren, se resuelven de manera rápida y eficiente.
Pasos para crear un plan de control de motores:
- Realice un inventario de todos los motores de la instalación.
- Cree una lista de motores con sus principales parámetros, condición técnica, vida útil.
- Desarrolle instrucciones generales para realizar reparaciones.
- Desarrollar pautas para mantenimiento preventivo, lubricación e inspección.
- Cree un stock de seguridad de repuestos de uso frecuente.
- Cree una especificación de compra para motores nuevos.
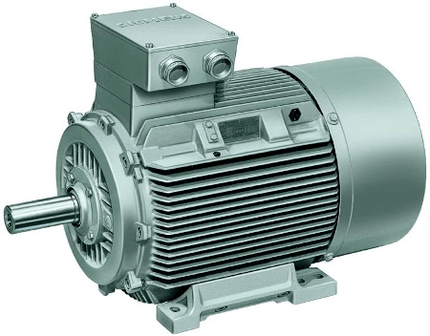
Rebobinado de motores eléctricos
Generalmente, rebobinar un motor eléctrico viejo es mucho más económico que comprar uno nuevo.
El motor eléctrico debe reemplazarse si el costo de rebobinarlo supera el 60% del costo de uno nuevo.
Entonces todo dependerá de cómo se realice el rebobinado.
Si el trabajo se realiza al nivel más alto, el motor perderá solo el 1% -2% por ciento de su eficiencia.
Si el rebobinado se realiza mal, las pérdidas en el motor eléctrico aumentarán entre un 5% y un 10%.
Reemplazar el motor eléctrico antiguo por uno nuevo de bajo consumo tiene sentido en los casos en que el motor funciona más de 2000 horas al año.
El período de recuperación de la inversión para un nuevo motor de bajo consumo energético no será superior a 1, 5 - 2 años.
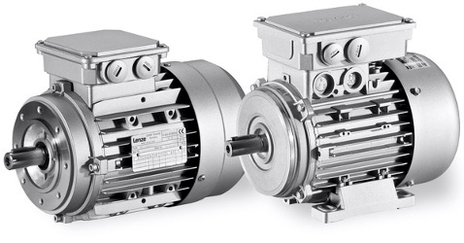
Ahorro energético en la empresa aumentando el factor de carga
El factor de carga es la relación entre la potencia operativa y la potencia aparente.
Así de eficientemente se utiliza la energía.
Cuanto mayor sea el factor de carga, más eficientemente se utilizará la electricidad.
El motor eléctrico funciona de manera óptima al 75% de carga o más.
Por lo tanto, instalar motores por encima de la potencia requerida (por razones de seguridad) no solo será más costoso, sino también ineficiente en términos de consumo de energía.
El factor de carga se puede aumentar de la siguiente manera:
- parada de motores descargados,
- sustitución de motores, que se cargan en menos del 45%, por modelos menos potentes,
- redistribución de la carga entre los motores eléctricos existentes.
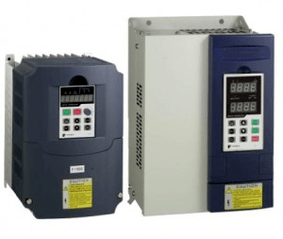
Unidad de frecuencia variable (VFD)
La instalación de variadores de frecuencia solo tiene sentido para sistemas dinámicos.
En sistemas estáticos, que están involucrados, por ejemplo, solo para levantar cargas, la instalación de un variador de frecuencia no ayudará y, a menudo, puede dañar.
El VFD equilibra la carga y la velocidad del motor, lo que garantiza que la energía eléctrica se utilice de manera óptima.
El VFD puede reducir el consumo de energía del motor en un mínimo del 5% y un máximo del 60%.
El período de recuperación de la inversión de VFD suele ser de 1 a 3 años.
Optimización de sistemas de aire comprimido
El aire comprimido se utiliza en una amplia variedad de industrias.
En algunas empresas, el aire comprimido es el principal consumidor de electricidad.
El aire comprimido se utiliza en dispositivos y equipos neumáticos, en transportadores, líneas automáticas.
El uso de aire comprimido es popular porque es una fuente de energía conveniente y segura.
Pero muchas personas olvidan que el aire comprimido es una de las fuentes de energía más ineficientes: solo el 5% de la electricidad gastada en la producción de aire comprimido se convierte en trabajo útil, el 95% restante sale a la tubería.
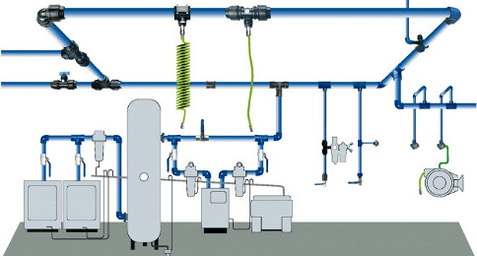
Ahorro de energía en la empresa: aire comprimido:
- No utilice aire comprimido para limpiar el local.
- La reducción de la temperatura del aire en la entrada del compresor en un 3% reduce el consumo de energía en un 1%.
- Para esos procesos técnicos, cuando sea posible, reduzca la presión del aire comprimido al mínimo. Bajar la presión en un 10% reduce el consumo de energía en un 5%.
- Realice inspecciones periódicas, reparaciones de equipos de compresores y líneas de transmisión de aire comprimido. Uno, incluso la fuga más pequeña de aire comprimido, puede reducir la eficiencia del equipo en ocasiones.
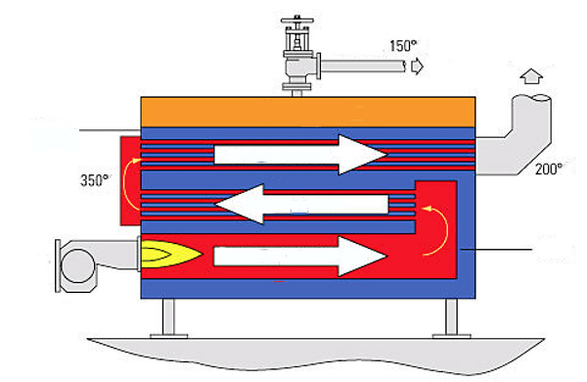
Ahorro de energía en la empresa: reducimos las pérdidas de calor y vapor
El vapor se utiliza a menudo en la industria, especialmente en las industrias textil, alimentaria y de procesamiento.
Mejorar la eficiencia de las calderas de vapor y reutilizar el calor generado puede reducir significativamente el consumo de energía en estas plantas.
Producción de vapor
La caldera funciona de manera más eficiente a plena potencia.
Debido al hecho de que la demanda de la cantidad de vapor puede cambiar con el tiempo, a menudo sucede que la caldera funciona por debajo de su carga óptima.
La capacidad de la caldera instalada puede ser mucho mayor que las necesidades de la empresa, debido a una caída en la demanda de productos o planes no realizados para expandir la producción.
Además, la capacidad de la caldera puede no ser necesaria debido a mejoras en el proceso de producción o la introducción de medidas de ahorro energético.
En tales casos, la caldera no funciona a plena capacidad o en el modo de ciclos cortos de encendido y apagado.
Ambas situaciones conllevan importantes pérdidas de energía.
No existen soluciones sencillas y económicas para este problema.
La opción más sencilla esinstalar una caldera "pequeña" que funcione a plena capacidadcon una carga de trabajo media o baja en la empresa.
A pesar de que esta no es una solución barata, el período de recuperación de dicha inversión puede ser inferior a dos años.
Y, en general, siempre es más eficiente tener varias calderas pequeñas intercambiables, especialmente en empresas con demanda cambiante o fluctuaciones estacionales significativas en el consumo de calor y vapor.
Sistema de regulación automática
Si la empresa tiene varias calderas, entonces tiene sentido instalarsistema automático para regular la carga de las calderas. . .
La automatización responde a la necesidad de vapor en la empresa, redistribuyendo la carga entre las calderas, enciende o apaga las calderas, aumentando así significativamente la eficiencia de todo el sistema.
Válvula de compuerta
En empresas donde las calderas se cierran regularmente debido a una caída en la demanda de vapor, las pérdidas de calor a través de la chimenea pueden ser bastante altas.
Es posible bloquear la pérdida de aire caliente a través de la chimenea.instalando una válvula de compuertaque cierra la tubería cuando la caldera está apagada.
Prevención y mantenimiento
Si se dejan desatendidos, los quemadores y los sistemas de retorno de condensado pueden deteriorarse o fallar rápidamente.
Esto puede reducir la eficiencia de la caldera en un 20% -30%.
Un programa de mantenimiento simple, asegurando que todos los componentes de la caldera estén funcionando a su nivel máximo, aumentará significativamente la eficiencia operativa.
En la práctica, el mantenimiento regular reduce el consumo de energía de la caldera en un 10%.
Aislamiento: la pérdida de calor de la superficie de una caldera debidamente aislada debe ser inferior al 1%.
Eliminación de hollín y sarro
Es necesario monitorear constantemente y eliminar la formación de hollín en los tubos de la caldera, incrustaciones dentro de la caldera.
Una capa de hollín de 0, 8 milímetros de grosor reduce la transferencia de calor en un 9, 5%, mientras que una capa de 4, 5 milímetros de grosor reduce la transferencia de calor en un 69%.
Las incrustaciones se forman cuando se depositan calcio, magnesia y silicio en el intercambiador de calor de la caldera.
La escala de 1 milímetro de espesor aumenta el consumo de energía en un 2%.
El hollín y las incrustaciones se pueden eliminar mecánicamente o con ácidos.
La formación de hollín e incrustaciones puede determinarse mediante un aumento de la temperatura de los gases de combustión o mediante una inspección visual cuando la caldera no está en funcionamiento.
La formación de hollín y sarro debe controlarse con especial atención si la caldera funciona con combustibles sólidos (carbón, turba, leña).
Las calderas de gas son menos propensas a los problemas de hollín.
Optimización de la purga de calderas
La purga de la caldera es la descarga de agua de la caldera para limpiar el agua dentro de la caldera de impurezas y sales.
El propósito de la purga de la caldera es evitar o reducir la formación de incrustaciones.
Una purga insuficiente de la caldera puede provocar la entrada de agua en el vapor o la formación de depósitos en la caldera.
Una purga excesiva significa pérdida de calor, agua y productos químicos.
El nivel óptimo de purga depende del tipo de caldera, la presión de funcionamiento en la caldera, la preparación y la calidad del agua utilizada.
Lo primero a lo que hay que prestar atención es la preparación del agua. Si el agua está bien tratada (bajo contenido de sal), la tasa de purga puede ser del 4%.
Si hay sustancias extrañas y sales en el agua, la tasa de purga será del 8% al 10%.
El sistema de purga automática también puede reducir significativamente el consumo de energía.
El período de recuperación de la inversión para un sistema de este tipo suele ser de 1 a 3 años.
Reducción de emisiones de humo
El humo excesivo a menudo es el resultado de la penetración de aire en la caldera y la chimenea a través de fugas y aberturas.
Esto reduce la transferencia de calor y aumenta la carga en el sistema del compresor.
Las fugas y los agujeros se pueden eliminar fácilmente, solo es necesario realizar periódicamente una inspección visual de la caldera y la chimenea.
Regulación de aire
Cuanto más aire se utiliza para quemar combustible, más calor se lanza al viento.
Una cantidad de aire ligeramente superior a la relación estequiométrica ideal de combustible / aire es necesaria por razones de seguridad, para reducir las emisiones de NOx, y depende del tipo de combustible.
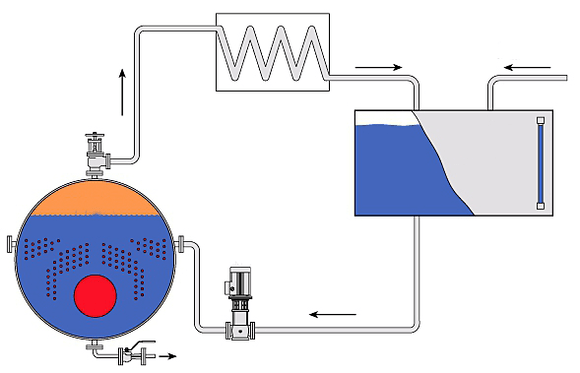
Las calderas en malas condiciones técnicas pueden utilizar hasta un 140% de aire adicional, lo que resulta en emisiones de humos excesivas.
Un quemador de gas eficiente requiere del 2% al 3% de oxígeno suplementario, o del 10% al 15% de aire suplementario, para quemar el combustible sin generar monóxido de carbono.
La regla general es que la eficiencia de la caldera aumenta en un 1% por cada 15% de reducción de aire adicional.
Por lo tanto, es necesario verificar constantemente la relación aire / combustible.
Este evento no cuesta nada, pero tiene un efecto muy bueno.
Monitoreo de emisiones de humo
La cantidad de oxígeno en el gas de combustión es la suma de aire adicional (agregado para aumentar la seguridad y reducir las emisiones) y aire que se filtra en la caldera a través de orificios y fugas.
La presencia de fugas y agujeros se puede detectar fácilmente si se establece un sistema de monitoreo para el aire entrante y la cantidad de oxígeno en los gases de combustión.
Utilizando los datos sobre la cantidad de monóxido de carbono y oxígeno, es posible optimizar la relación combustible / aire en la caldera.
La instalación de un sistema de seguimiento y análisis de las emisiones de humos suele amortizarse en menos de un año.
Ahorro de energía en la empresa: instalación de un economizador
El calor de los gases de combustión se puede utilizar para calentar el agua que entra en la caldera.
El agua calentada ingresa a la caldera y requiere menos calor para convertirse en vapor, lo que ahorra combustible.
La eficiencia de la caldera aumenta un 1% por cada 22 ° C de disminución de la temperatura de los gases de combustión.
El economizador puede reducir el consumo de combustible entre un 5% y un 10% y se amortizará en menos de 2 años.
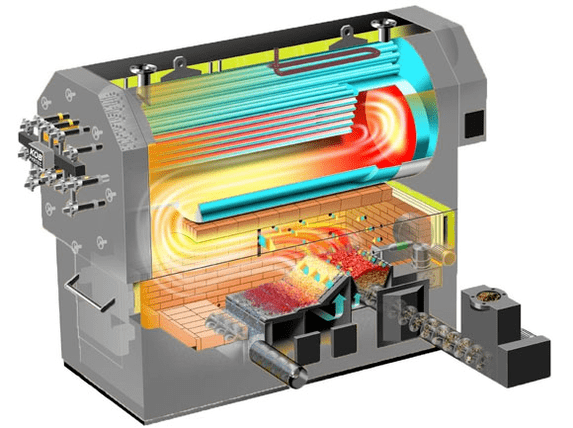
Intercambiador de calor para extraer calor del agua y vapor de la purga de la caldera
El intercambiador de calor ayudará a reciclar aproximadamente el 80% del agua y el calor del vapor de la purga de la caldera.
Este calor se puede utilizar para calentar edificios o para calentar el agua que alimenta la caldera.
Cualquier caldera con una tasa de purga constante del 5% o más es un excelente candidato para un intercambiador de calor.
Si el sistema de purga no funciona en modo constante, entonces tiene sentido pensar en transferirlo a un modo constante mientras se instala simultáneamente un intercambiador de calor.
El período de recuperación promedio de un intercambiador de calor no excederá de 1, 5 a 2 años.
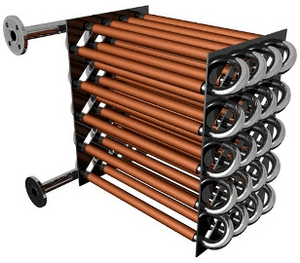
Instalación de un economizador de condensación
El condensado caliente se puede devolver a la caldera, lo que ahorra energía y reduce la necesidad de agua tratada.
El economizador de condensación puede aumentar la eficiencia del sistema en un 10% adicional.
La instalación de dicho economizador debe llevarse a cabo bajo la estrecha supervisión de especialistas que tendrán en cuenta todos los matices de dicho sistema, su efecto en la caldera y la composición química del agua.
El uso de un sistema que devuelve el condensado a la caldera generalmente se amortiza en 1-1. 5 años.
Un sistema que dirige el condensado a un suministro de agua caliente se amortiza en menos de un año.
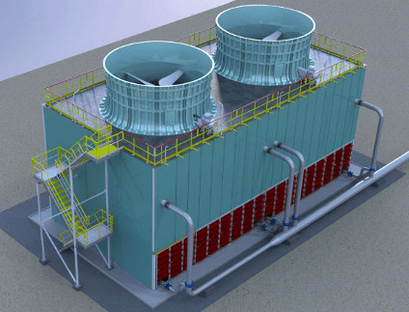
Torres de enfriamiento (torres de enfriamiento)
Una torre de enfriamiento es un intercambiador de calor en el que el agua se enfría mediante una corriente de aire.
Y en términos de eficiencia energética, una torre de enfriamiento es un dispositivo que arroja calor al viento.
Potencial de ahorro energético en torres de refrigeración:
- En algunas empresas tiene sentido abandonar por completo las torres de refrigeración. Hay muchos casos en los que se utiliza calefacción para calentar una habitación y al mismo tiempo se utiliza una torre de refrigeración para disipar el calor. La instalación de una bomba de calor resolverá el problema de la calefacción y reducirá al menos parcialmente la necesidad de usar la torre de enfriamiento.
- La instalación de disyuntores para los ventiladores de las torres de refrigeración puede reducir el consumo de energía en un 40%.
- Reemplazar los ventiladores de aluminio o hierro por ventiladores nuevos (de fibra de vidrio y plástico moldeado) puede reducir el consumo de energía hasta en un 30%.
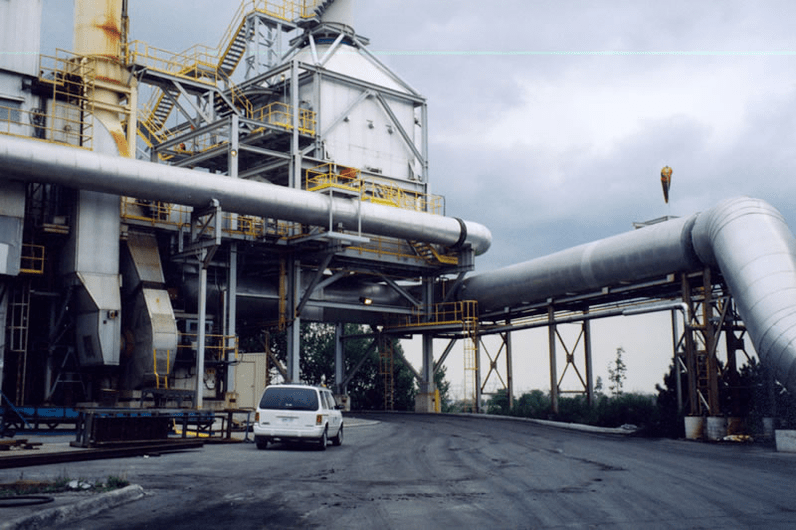
Reducción de pérdidas en líneas de vapor
Desconexión de líneas de vapor no reclamadas
Las necesidades y el consumo de vapor cambian constantemente.
Esto puede llevar al hecho de que todo el sistema de distribución de vapor no se use a plena capacidad, sino solo del 20% al 50%, lo que inevitablemente conduce a pérdidas de calor.
Está claro que optimizar o reconfigurar todo el sistema de distribución de vapor para satisfacer nuevas necesidades será muy costoso y, quizás, no factible.
Sin embargo, identificar y cerrar las líneas de vapor que apenas se utilizan puede ser una medida de ahorro energético muy eficaz.
Ahorro de energía en la empresa - Aislamiento térmico de tuberías
Las tuberías de vapor aislantes pueden reducir las pérdidas de energía hasta en un 90%.
Este es uno de los ahorros de energía más rápidos en un sistema de distribución de vapor.
El período de recuperación promedio para el aislamiento de tuberías a través de las cuales se transmite vapor o agua caliente es de aproximadamente 1 año.
Tuberías de condensado durante 1, 5-2 años.
Monitorización de trampas de vapor
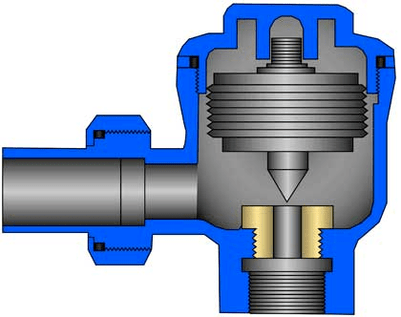
Un simple programa de monitoreo del estado técnico de las trampas de vapor puede reducir significativamente la pérdida de calor.
Por ejemplo, si no se ha realizado el mantenimiento durante 3 a 5 años, entonces, como regla, alrededor de un tercio de las trampas de vapor están fuera de servicio, lo que permite que el vapor se filtre en el sistema de drenaje de condensado.
En la práctica, en las empresas que tienen un programa de monitoreo de trampas de vapor, no más del 5% de las trampas de vapor están en una condición defectuosa.
El período promedio de recuperación de la inversión para el reemplazo o el mantenimiento de un purgador de vapor es de menos de seis meses.
Un programa de monitoreo de trampas de vapor generalmente reducirá las pérdidas de vapor en un 10%.
Purgadores de vapor termostáticos
El uso de trampas de vapor termostáticas modernas puede reducir el consumo de energía y al mismo tiempo aumentar la confiabilidad de todo el sistema.
La principal ventaja de las trampas de vapor termostáticas es que
- abierto cuando la temperatura se acerca al nivel de vapor saturado (+/- 2 C °),
- emiten gases no condensables después de cada apertura y
- están en estado abierto al comienzo de la operación del sistema, lo que asegura su rápido calentamiento.
Además, estas trampas de vapor son muy fiables y se pueden utilizar en una amplia gama de presiones.
Desconectar trampas de vapor
Puede reducir el consumo de energía apagando las trampas de vapor en las líneas de vapor sobrecalentado cuando no estén en uso.
Eliminación de fugas de vapor
Un programa de reparación de fugas de vapor en orificios pequeños puede dar sus frutos en menos de 3 a 4 meses.
No debemos olvidar que las pequeñas fugas pueden pasar desapercibidas durante años, dañando constantemente el sistema.
Reutilización de condensado y vapor
Cuando una trampa de vapor descarga condensado de un sistema de vapor, la caída de presión crea vapor a partir de ese condensado.
Este vapor, junto con el condensado, se puede utilizar en un intercambiador de calor para calentar el agua o el aire de alimentación.
Lo más importante es que es posible usar este vapor y condensado cerca del punto de liberación, ya que puede ser muy costoso crear un sistema de tuberías separado para transportarlo al punto de uso.